*publi-rédactionnel
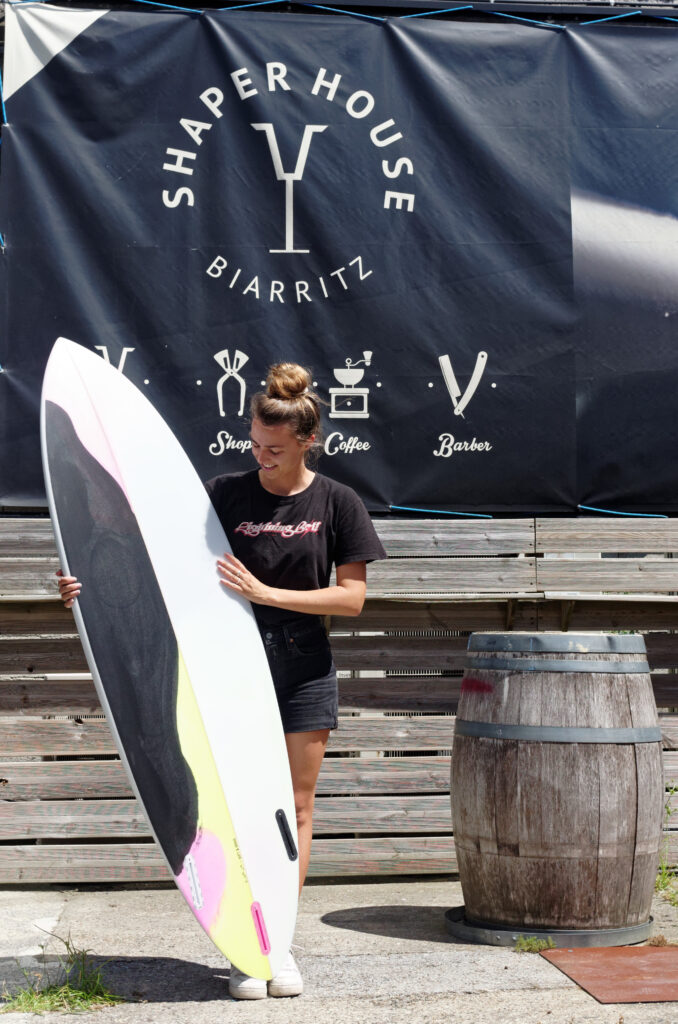
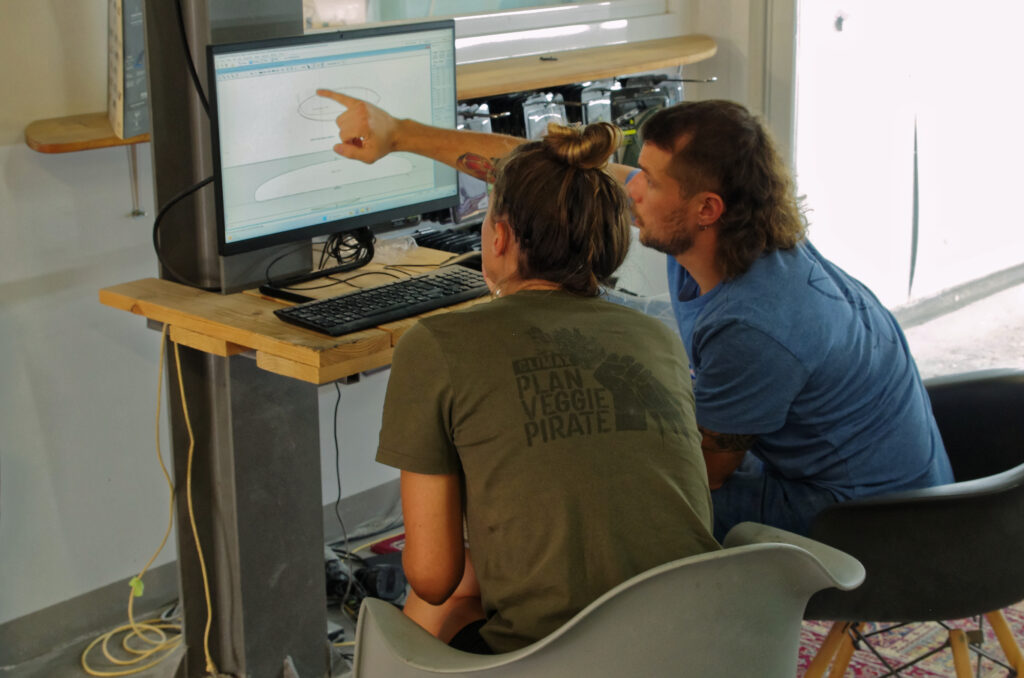
Le surf est un vivier d’expériences, qui tranchent du rythme quotidien pour venir éveiller des sensations nouvelles. Si la glisse peut se profiler sous bien des formes (lire aussi : Retour d’expérience : première fois en foil), c’est cette fois aux formes elle-même que je me suis intéressée. Direction une activité manuelle, aux origines artisanales : le shape.
Une première oui, mais une première bien accompagnée quand même, pour espérer surfer la planche sortie de l’atelier, et pas voir flotter une saucisse mal coupée ! Pour ce saut dans le grand bain, j’ai pris la direction de la Shaper House, à Biarritz, qui propose un format tout compris pour faire sa planche de surf, soi-même. L’espace conçu entièrement autour de l’univers shape met à disposition les outils nécessaires (nombreux et spécifiques) mais aussi la matière première (pain de mousse, résine, fibre de verre, consommables et matériel de protection…), des salles de shape optimisées, où travailler confortablement et surtout des professionnels présents étape par étape pour vous encadrer.
Pré-shape
Des étapes, il y en a plus d’une pour shaper sa planche ! Avant d’aller en salle de shape, je suis accueillie par Vadim, qui m’a accompagnée sur le début de ma création. Pour cette première, je ne suis pas partie d’un pain de mousse brut, mais ai fait l’usage d’un pré-shape, conçu en 3D sur le logiciel français « Shape 3D », largement répandu dans le domaine du shape professionnel. Premier choix déterminant donc : le modèle.
« J’ai un niveau intermédiaire, et surfe encore sur des planches plutôt mid-lengh, assez litrées. Dernièrement j’ai délaissé ma 7’0 de 52 litres pour apprivoiser ma 6’8 de 43L. Je voudrais donc shaper ma prochaine planche, plus courte, qui me permettra plus de maniabilité à l’eau, à mesure que ma progression me permettra de m’essayer à davantage de manoeuvres. » Voilà ce que j’ai dis globalement à Vadim, sûrement de façon moins claire et plus fouillis. Le professionnel m’a aiguillé sans soucis sur le modèle pré-enregistré le plus proche de mes besoins, que nous avons retravaillé sur le logiciel. Pour ma part, ce sera une 6’0, dont l’outline (découpe de la planche vue de face) rappelle le modèle Hypto Krypto de Haydenshapes ou encore le Sixtyniner de Pukas.
Ce moment a été aussi l’occasion de passer en revue certains termes et de comprendre comment fonctionne une planche. Globalement, plus il y a de surface sur l’eau plus il y a de vitesse, mais la réduction du volume au nose et au tail permet de franchir les sections et d’attaquer les courbes. De la même façon, un rail plus épais aidera à la flottaison et à la vitesse mais sera plus difficile à tourner. C’est donc là tout l’art du shape : trouver l’équilibre. Au niveau de la carène (le dessous de la planche), l’arrondi creusé appelé le concave va servir à canaliser l’eau, en créant un effet de ventouse qui va aider le rail, les deux étant connectés. Au niveau du tail de ma planche, nous avons donc opté pour un double concave, permettant un point de pivot central pour tourner mais aussi plus de contrôle et de prise de vitesse.
Une fois mon design prêt dans Shape 3D, il a été usiné en machine KKL sur un pain PU 6’4 (lire aussi : PU versus EPS : quel matériau choisir pour votre planche de surf ?). En 30 minutes, il en sortait déjà une belle forme sur laquelle se mettre au travail !
Shaper : travailler la surface et les rails
Rapidement, je mets la main à la pâte. Il faut d’abord faire la finition du préshape, en enlevant les traces de fraise de la machine par le ponçage. Vadim me détaille les gestes, les points de vigilance et m’indique les outils. Je ponce d’abord avec un gros grain, puis avec un grain plus fin et une cale plus souple à mesure qu’on se rapproche du rendu souhaité. Le travail sur les rails doit se faire minutieusement, pour affiner leurs formes et parfaire l’arrête du edge : on travaille d’abord le haut du rail, avant de s’attaquer à la tranche avec une grille à poncer.
De la couleur ? Bien sûr !
Une fois la surface lissée, j’ai pu penser à imaginer le rendu final en venant au masquage. C’est l’étape où l’on place les scotchs délimitant les zones où la couleur sera placée. Cette étape vient avec le plaisir de pouvoir exprimer sa créativité, en imaginant une ou plusieurs couleur et une disposition de ces dernières 100% personnalisée, à son image. Les lumières latérales et rasantes de la salle de shape se rendent ici très utiles, car ce sont les ombres formées sur la planche qui permettent de guider la pose du scotch le plus droit possible. Le geste est technique et doit se faire de façon fluide, en utilisant ses deux mains (l’une tire, l’autre colle). À nouveau, Vadim me montre la marche à suivre et s’assure que j’y parvienne ensuite par moi-même. Je colle deux scotchs, un premier bien collant et solide qui marquera une limite claire, puis un second plus souple (qu’on ne rabat pas) et sur lequel la résine coulera vers le sol (et non sur l’autre face de la planche).
Pour ma part, j’ai choisi de faire un mélange de couleurs vives et de noir sur seulement une moitié du dessous de ma planche. J’ai donc posé la couleur directement sur la mousse. Sylvain, qui m’a aidé dans la suite de ma création, a fait pour moi les mélanges pour les trois couleurs choisies : rose flashy, jaune fluo et noir mat. J’ai ensuite fait couler les couleurs une à une selon l’inspiration : une étape sous pression tant on n’a pas envie de se louper et pas de marge d’erreur !
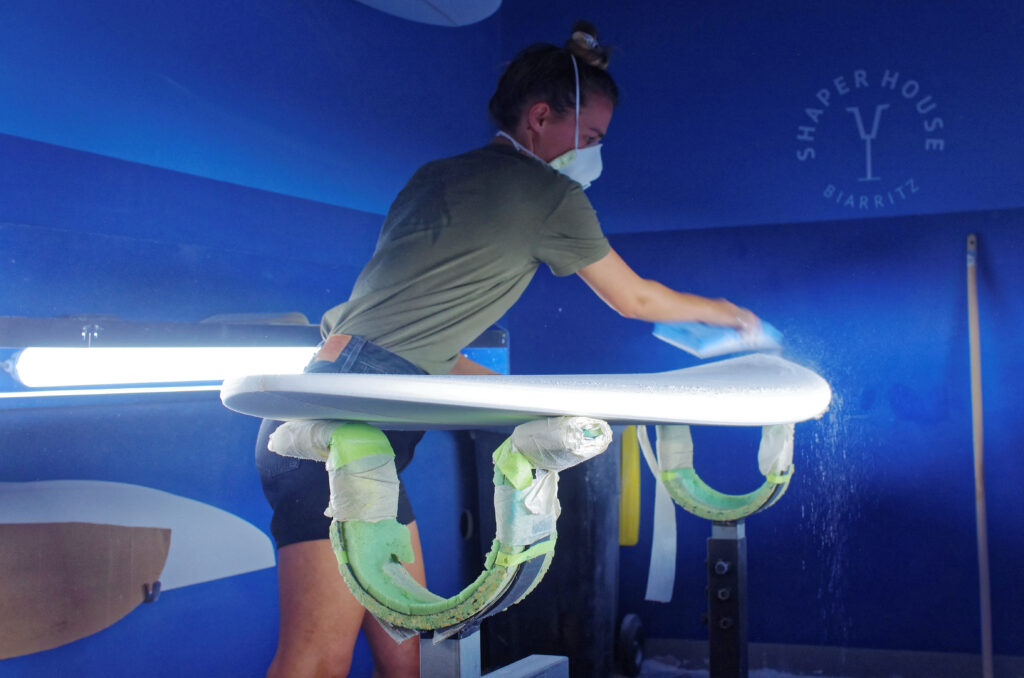
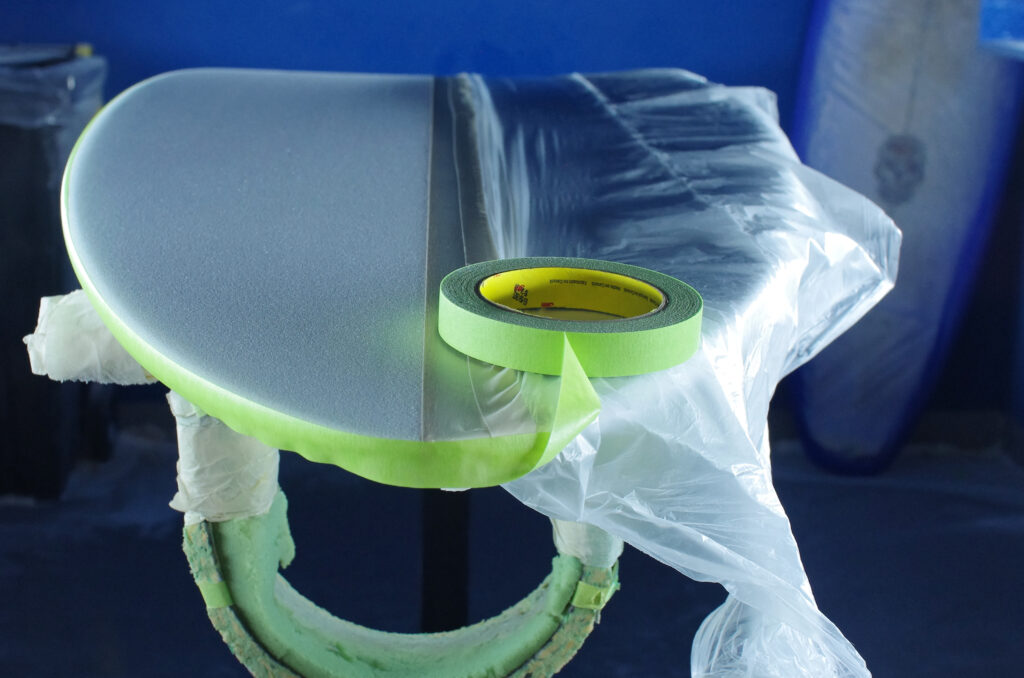
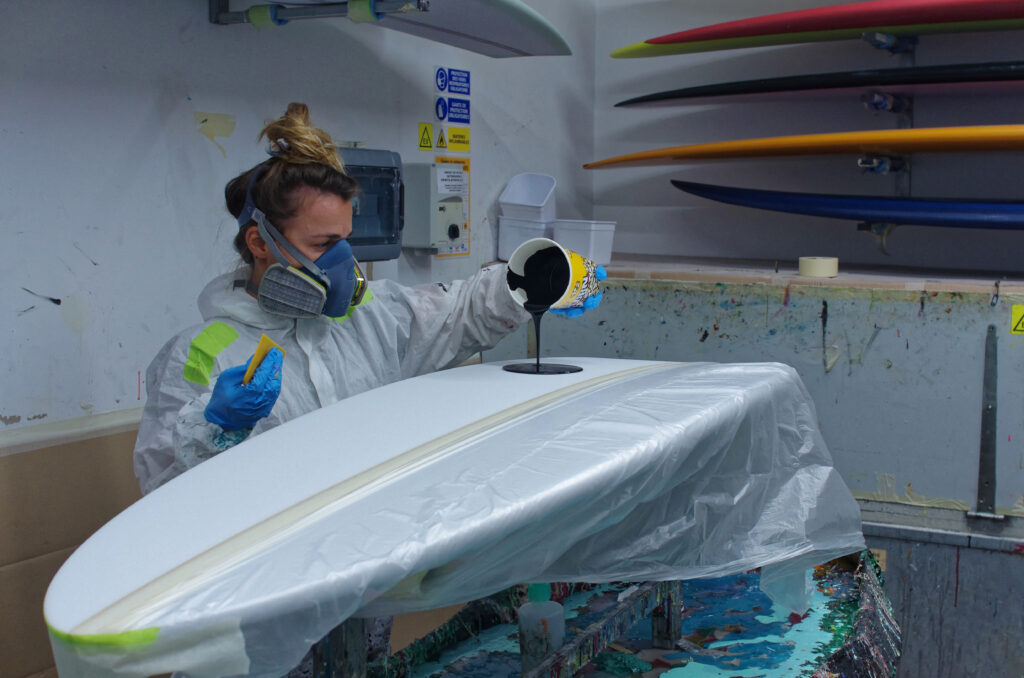
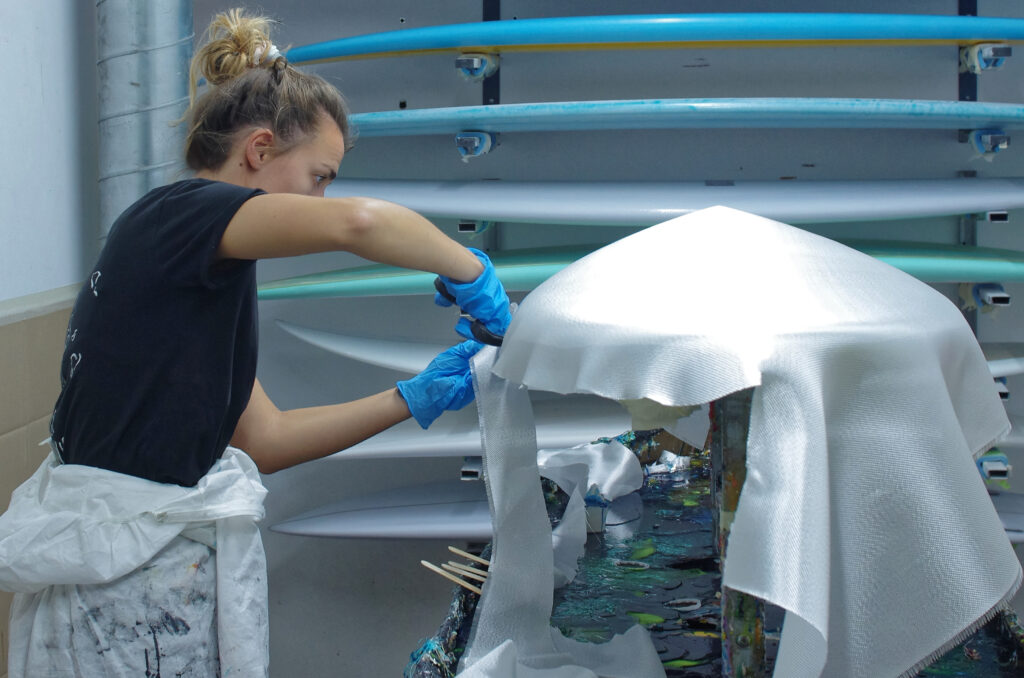
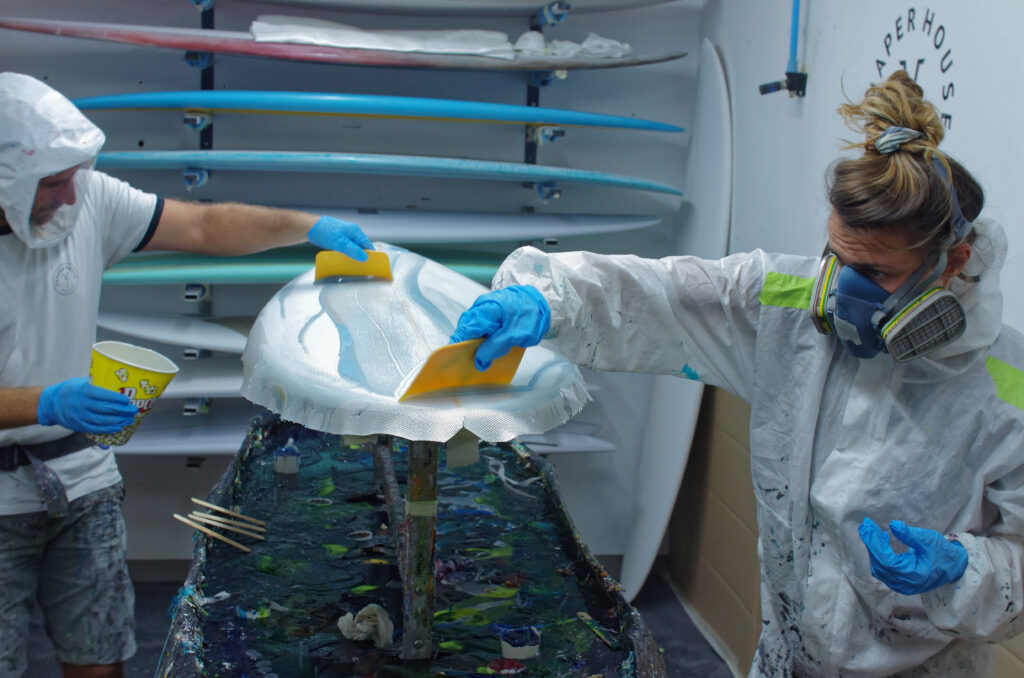
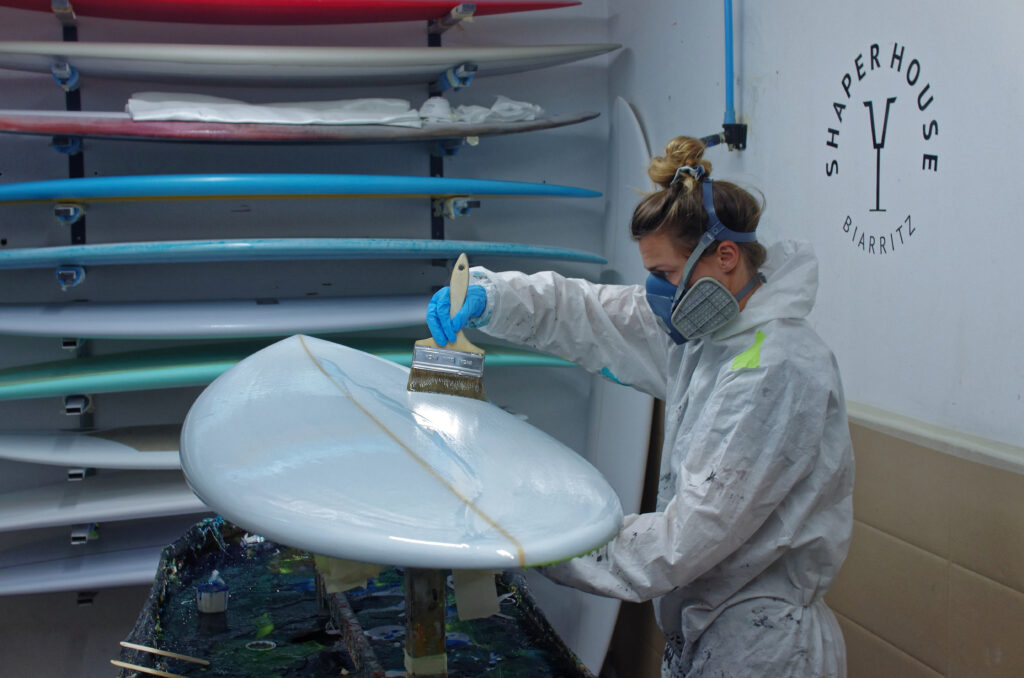
Glassing : être à la fois rapide et patient
La phase de stratification vient une fois que la couleur a séchée. Elle s’effectue en plusieurs étapes, puisqu’il faut travailler une face de la planche après l’autre. À cette étape, il faut tirer la fibre de verre sur la planche, puis la couper pour éliminer le surplus sur les bords.
Au dos, nous choisissons une épaisseur de 6oz, pour donner de la structure au pain en créant une coque solide qui protègera la mousse. Ensuite on vient « filer » (faire couler) la résine sur la matière, que l’on étale à l’aide d’un « squeegee« , une sorte de spatule plate sans manche. La résine joue ici le rôle de liant entre le pain de mousse et la fibre de verre. Elle a des caractéristiques mécaniques permettant la solidité du produit final. J’avance en miroir avec les gestes habitués de Sylvain, qui s’assure du rendu et ajuste les miens au besoin. Dans le cas d’une planche à colorer cette résine peut-être teintée mais dans mon cas elle est restée neutre.
Sur les bords (« laps ») de la planche, on vient ensuite faire un « filler » qui permettra de poncer légèrement la zone de superposition entre les tissus du bottom et du pont.
Je répète ensuite le même processus sur le dessus de la planche, en choisissant cette fois sur les conseils de Sylvain une couche de fibre de verre de 6oz doublée d’une couche de 4oz pour trouver un équilibre entre la solidité nécessaire pour éviter les enfoncements et le poids ajouté par la matière. La résine séchant vite, il faut mettre du rythme dans cette étape.
L’ajout d’un photo initiateur UV dans le mélange de résine permet de passer la planche dans un « four » à néons UV, accélérant le séchage (un petit luxe !). Après 10 minutes, j’ai pu appliquer le hotcoat. Cette étape se fait sur l’intégralité des surfaces, des deux côtés de la planche, rails compris. Il s’agit de résine catalysée associée à un styrène paraffiné, permettant un aspect lisse de surface et facilitant le ponçage final.
Les dérives
Vient la pose des plugs de dérive et la découverte d’une nouvelle machine : une affleureuse. Je viens d’abord tracer les lignes à suivre à la découpe, sous l’oeil vigilant de Vadim, en prenant en compte l’orientation des dérives. Ensuite, la machine entre mes mains creuse dans la mousse une ligne droite, à deux profondeurs définies par deux fraises distinctes et adaptées aux plugs choisis (pour ma part des Futures en thruster). Une fois les fentes creusées, on vient vérifier que l’inclinaison des dérives à 6,5° est respectée et on réajuste au besoin.
Petite particularité, selon le fournisseur de dérives cette dernière n’est pas placée au même endroit. Chez FCS, on trouve l’inclinaison dans le boitier tandis que chez Futures on la retrouve dans la dérive.
Je viens ensuite couler de la résine dans les trous et sur des patchs de fibre de verre par dessus les plugs, pour fixer solidement l’ensemble.
Poncer, poncer, poncer
L’ultime étape est la phase de ponçage. Je travaille en miroir avec Vadim, qui me guide à nouveau sur les mouvements à appliquer et les outils qui se succèdent. Nous commençons à attaquer le hotcoat avec un socle dur et un disque à gros grain, puis enchainons avec un grain plus fin. Dans un troisième temps nous gardons le grain fin mais avec un socle mou, à mesure que l’on s’approche du niveau de finition souhaité : une fine couche de résine recouvrant la fibre de verre. Tout l’enjeu est ici de supprimer tout excédent de résine superflue, sans jamais toucher au ponçage la fibre de verre sous-jacente.
Bien que l’on pourrait penser cette étape plus comme une étape de force, elle est aussi minutieuse que les autres et demande tout autant d’attention. Pour ma part, c’est là que la boulette est arrivée : en appuyant trop fort au niveau de la latte, j’ai poncé un cran trop profond et rendu la latte apparente, ce qui a demandé une réparation avec un patch de résine pour éviter que ça ne prenne l’eau (je n’allais quand même pas faire un sans faute !).
Une fois poncée, la planche est nettoyée puis signée (on indique les côtes et on signe ce qu’on veut !). Puis on vient la vernir, pour un rendu propre et mat, définitif.
Shape & vibes
Parler de cette expérience sans parler de l’autour serait ne pas lui rendre justice, car ce qui l’a rendue unique et si plaisante, c’est aussi l’environnement ! Durant les deux jours et demis de cette initiation, j’ai partagé les lieux avec d’autres adeptes, novices ou professionnels, qui eux aussi avaient les mains dans les pots de résine (un coucou ici à Lolia et Pieric, qui se reconnaitront). À la Shaper House, on navigue entre les dérives et les planches en cours de création, dans l’odeur enivrante et rapidement familière de la résine et dans le bruit par moment d’une ponceuse ou d’une soufflette d’air comprimé. Entre chaque étape ou en attendant un temps de séchage, on passe une tête dans la salle d’à coté, on regarde le voisin ou la voisine à l’oeuvre et on s’inspire d’une idée, d’une couleur ou d’un modèle. On discute shape ou surf et on vanne sur la dernière boulette à rattraper autour d’un café. C’est aussi sérieux que joyeux et un bon moment en soi, avant même de penser à la finalité de l’opération.
Le surf
Ma beauté entre les mains, il a fallu attendre les 3 semaines préconisées pour lui permettre d’être à 100% sèche avant d’aller à l’eau. Au moment de la première session, ce sont beaucoup de sentiments mêlés : l’excitation de tester une nouvelle planche, la réalisation que celle-ci est née de mes mains à peine un mois avant et une petite appréhension de se dire « et si elle ne marche pas ? ». Mais une fois à l’eau, rien de tout ça. En dehors du fait que la planche soit pleinement fonctionnelle et réponde à mes attentes, il se crée aussi avec elle un lien en plus du reste de mon quiver. Je me sens connectée à cette planche et je lui fais confiance, je sens que je peux me fier à elle à 100%, car elle a été créée pour moi et par moi ! C’est aussi une fierté en plus de dire aux potes « c’est moi qui l’ai faite ». Bref, que du love. Une expérience 100% recommandée !
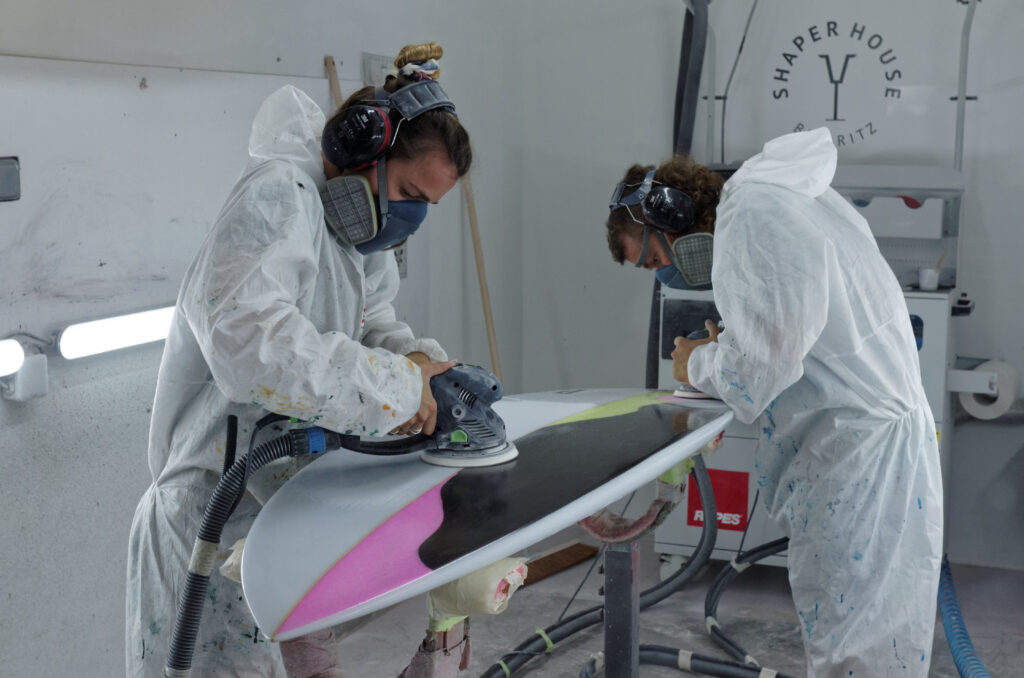
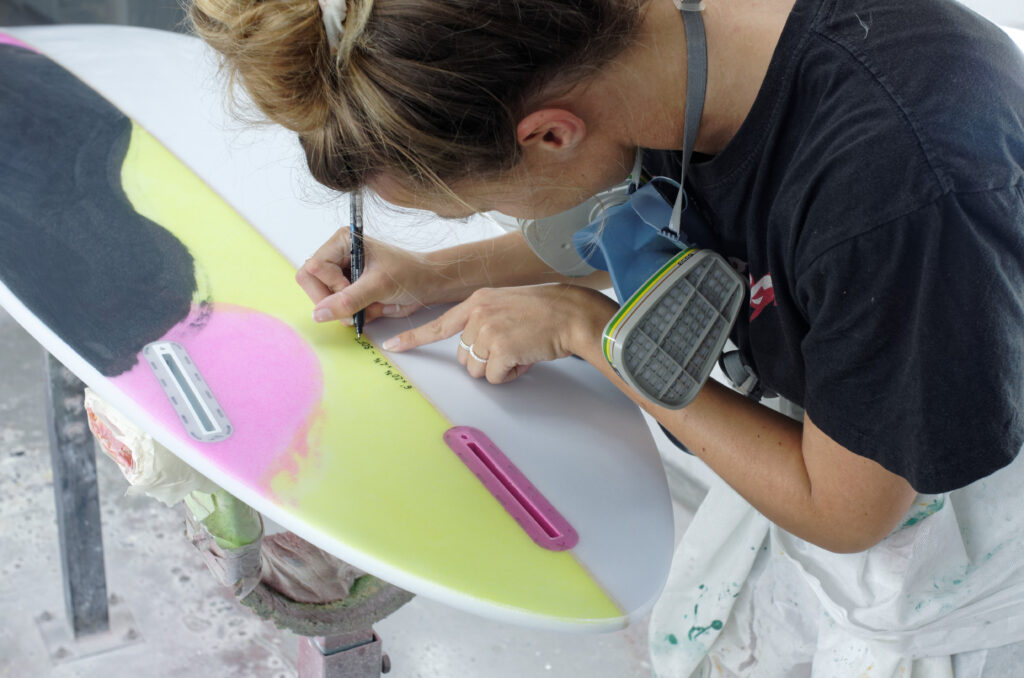
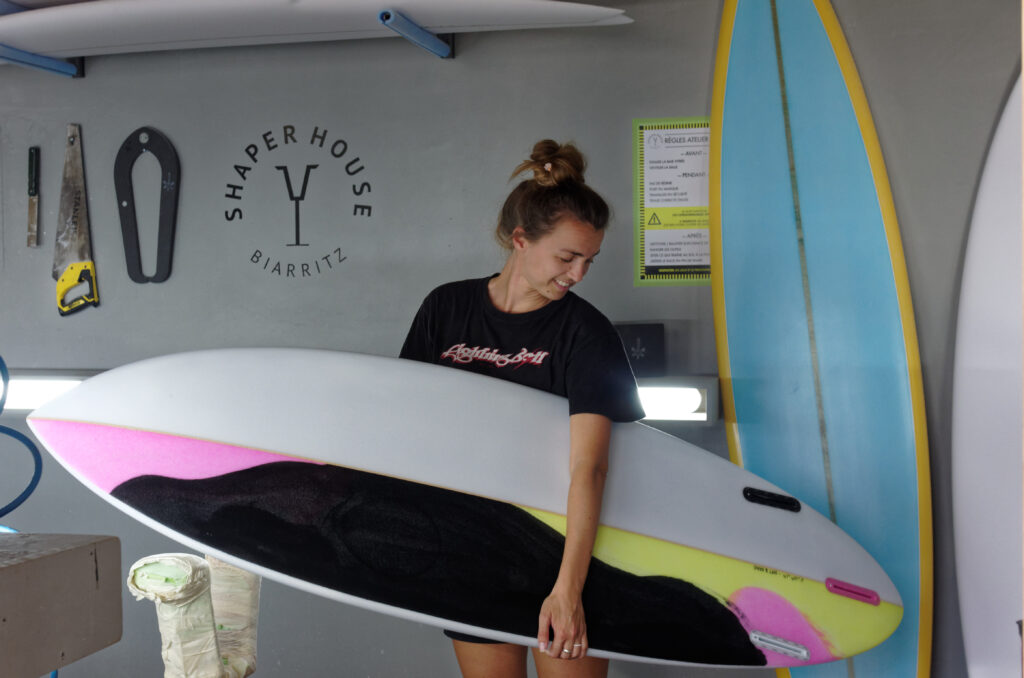